La fonderia in sabbia fa parte della metallurgia ed è una tecnica che permette di ottenere degli articoli metallici tramite la fusione dei metalli in specifiche forme in sabbia, dalla quale si ottengono le fusioni o getti. La fonderia è una delle tecniche più antiche per la lavorazione dei metalli (i primi manufatti ottenuti con questa tecnica risalgono infatti al 4000 a.C.) e consiste nell’immettere un metallo fuso in una cavità: una volta raffreddato si ottiene un pezzo che copia al positivo la forma della cavità. Al giorno d’oggi questi articoli metallici possono essere ricavati anche tramite operazioni di fucinatura, stampaggio o per asportazione di materiale da blocco. Nella maggioranza dei casi, tuttavia, il processo di fonderia risulta essere quello più economico, soprattutto se rivolto alla replica del pezzo in questione in piccole o medie serie. La fonderia è inoltre una tecnica molto versatile: con essa è possibile costruire pezzi con peso da pochi grammi a molte tonnellate.
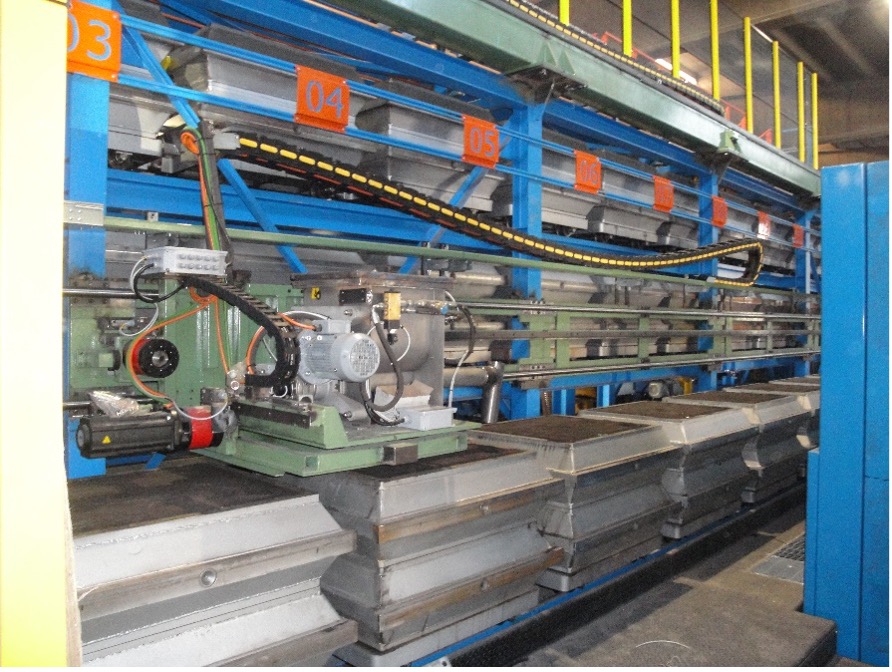
Il getto di fonderia
Il risultato del processo di fonderia è la fusione o getto. I pezzi fusi differiscono dal pezzo finale utilizzato in quanto necessitano di lavorazioni successive per ottenere precise quote e tolleranze, nelle quali viene eliminato l’impianto di colata. Sul modello dovrà essere previsto un sovra-metallo, pertanto, il getto di fonderia sarà sempre di dimensioni maggiorate rispetto al pezzo finito che si dovrà utilizzare. Un’ulteriore differenza tra il getto di fonderia e il pezzo finale da ottenere è data dalla presenza di inclinazioni dette angoli di sformo, derivanti dalla copia del modello da replicare.
Per arrivare dal getto di fonderia al disegno ideale del pezzo è necessaria la realizzazione di una forma del getto stesso, detta impronta, in un materiale adatto a contenere il metallo fuso. Il materiale più adatto allo scopo, più versatile ed efficace, anche in termini di costi, è la sabbia perché può prendere qualsiasi forma e ha una resistenza particolarmente alta al calore che ben si presta alla funzione richiesta.
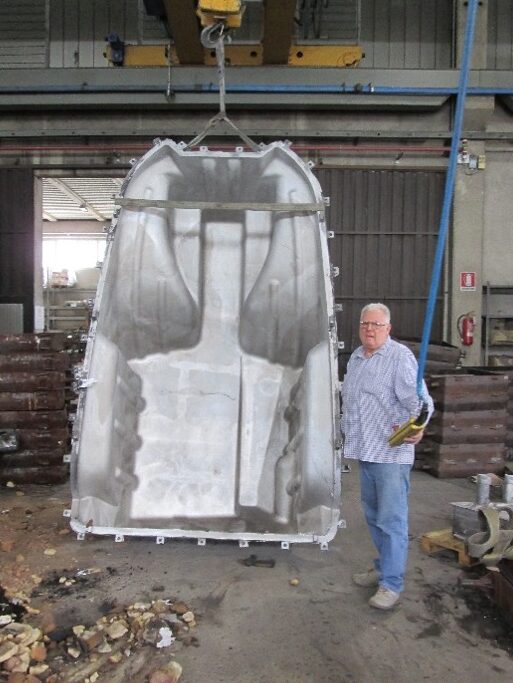
Il modello
Per creare un getto che abbia la forma esatta del pezzo da realizzare è necessario avere un modello che possa lasciare la sua impronta sulla sabbia, il quale verrà realizzato in un materiale diverso rispetto al metallo e più facile da lavorare. Solitamente vengono utilizzati legno o resine in blocco. Una volta creato, il modello verrà ricoperto di sabbia da fonderia.
Il materiale per la formatura più utilizzato, come si diceva in precedenza, è la sabbia perchè è plastica e facilmente demolibile, una volta riempito del metallo liquido e raffreddato. In fonderia vengono utilizzate delle specifiche tipologie e granulometrie di sabbia per ottenere forme di differenti qualità.
Una volta costruito, il modello dovrà avere alcune caratteristiche che non possono essere tralasciate onde evitare problemi durante il processo di fonderia. Tra queste, le principali sono:
• avere un corretto angolo di sformo sulle pareti verticali, per consentire che lo stesso modello possa essere estratto dalla sabbia una volta eseguita la forma e che nella sabbia rimanga l’impronta da riempire con il metallo fuso.
• Le raggiature: per una questione tecnologica insita nel processo fusorio non sono ottenibili angoli e spigoli vivi. Il modello deve avere dimensioni maggiorate rispetto al getto da ottenere perché, durante la fase di raffreddamento del metallo liquido, questo diminuisce di volume. Sarà compito di chi costruisce il modello aumentare le dimensioni in base al ritiro specifico del metallo scelto per produrre il getto di fonderia.
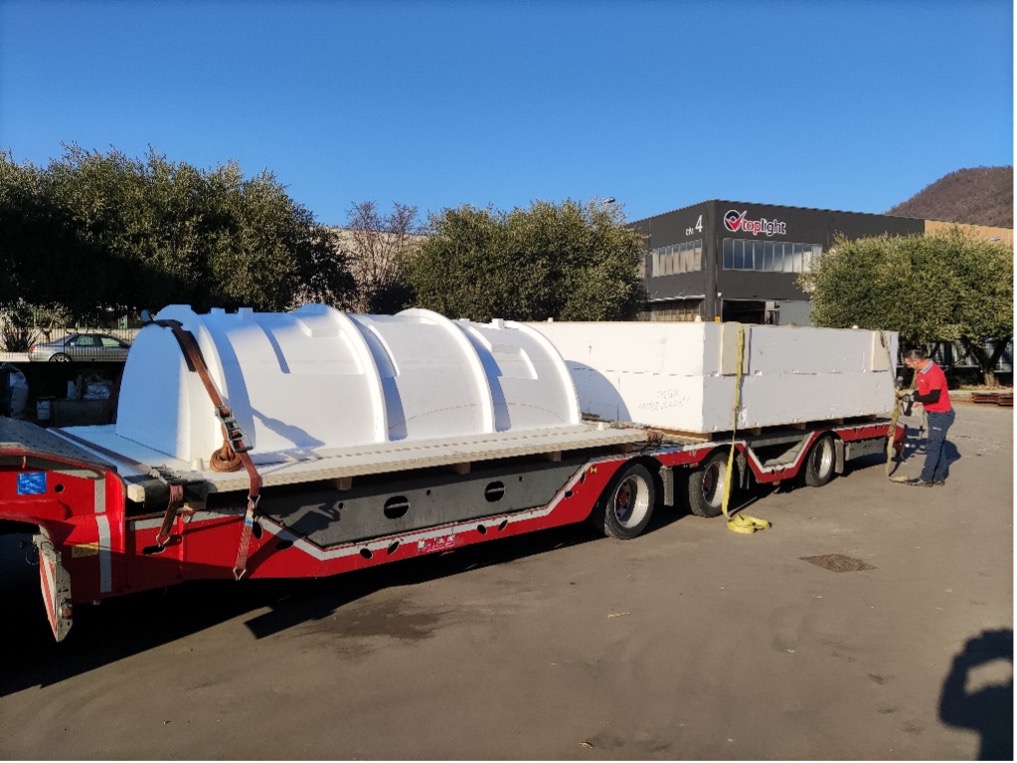
Le fasi finali
Per completare la formatura e ottenere una forma in sabbia pronta per la fusione, il fonditore dovrà dimensionare l’impianto di colata con cui riempirà la forma facendo in modo che il getto ottenuto sia privo di difetti visibili nonché di quelli interni occulti che si manifestano solo dopo lavorazione meccanica. Una volta completata la procedura di formatura si passerà alla fase di fusione: il metallo verrà fuso in un forno ad alta temperatura e versato nella cavità creata nella sabbia. Dopo la colata, il metallo viene lasciato raffreddare e solidificare all’interno dello stampo di sabbia. Le successive fasi sono: la demolizione dello stampo e l’estrazione del getto di fonderia, che successivamente verrà pulito, smaterozzato (tagliato l’impianto di colata) e sbavato per ottenere le dimensioni desiderate prima di essere inviato alla fase di lavorazione meccanica. Da quest’ultima si otterrà il pezzo finito pronto per l’utilizzo per il quale è stato progettato.
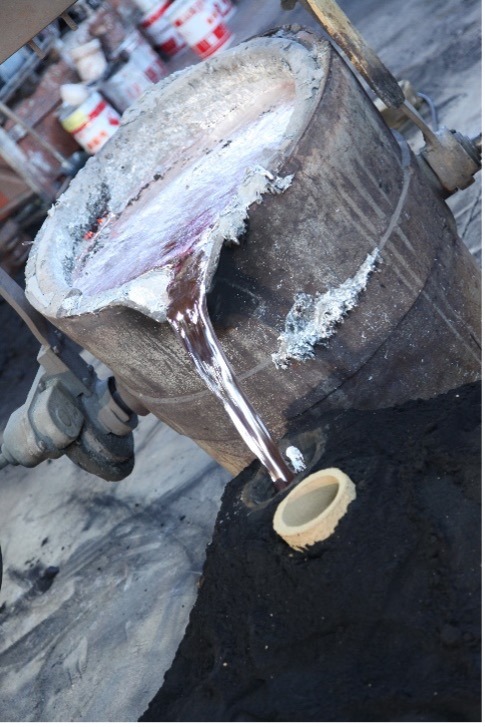